Finite Element Analysis (FEA) Essentials
Finite Element Analysis (FEA) Essentials
About the course
Learning Finite Element Analysis (FEA) can be challenging, with many resources focusing solely on theory or software. This course emphasizes understanding concepts and design choices in FEA. It covers different FEA approaches and the engineering judgment needed for model design, problem analysis, and result interpretation.
Key topics include stress definitions, model preparation, connection rigidity, boundary conditions, realistic load application, meshing, analysis, and post-processing. The course uses Femap with NX Nastran for demonstrations and examples, providing generic FEA considerations applicable to all software. It includes 8 online modules with 1-year unlimited access and a discussion forum.
Learning Outcomes
After these courses, you...• have a fundamental understanding of the important concepts involved with FEA,
• have improved your engineering judgement related to FEA,
• know the different considerations to make for preparation of your models,
• understand how best to implement Boundary Conditions and Loads,
• know the different element types and how they impact your meshing,
• know the limitations of different analysis types,
• understand typical post-processing steps,
• have seen 5 fully explained practical examples with video guides and solved with different approaches.
Who should attend this course
• Professionals of various industries involved with the execution of FEA projects.• Those managing or overseeing FEA related work that need to be able to provide judgement about the assumptions and choices made.
Prerequisites
• Technical background is required.• Basic experience with Finite Element Method software is beneficial.
Program & Details
-
Welcome
1. Welcome & Your instructor
2. Content overview
3. How to use this course -
Course 1 - Introduction to FEA
1. What is FEA for?
2. What does FEA do?
3. How to define a problem?
4. What is important in FEA
5. Consistent unit system
6. Conclusion -
Course 2 - FEA Important Engineering Concepts
1. What is stress?
2. Normal Stress and Shear Stress
3. Stress in 3D
4. Equivalent Stress
5. Hooke's Law
6. Structural Rigidity
7. Stress Concentrations
8. Active forces and reaction forces balance
9. Rigid Body Motion
10. Conclusion -
Course 3 - FEA Model Preparation
1. Importing CAD geometry
2. Creating geometry in preprocessor
3. Benefits of simplifying the geometry
4. Model Symmetry
5. How to define symmetry in FEA
6. Small details spoilmesh
7. How to connect beams to shells and beams/shells to solid
8. Rigid, semi-rigid and hinged connections in beam models
9. How to check if a connection is a hinge
10. How to calculate connection rigidity
11. Linear material properties
12. When linear material is not enough
13. Conclusion -
Course 4 - FEA Model Support & Boundary Conditions
1. Rigidity of supports
2. Realistic boundary conditions
3. Why pinned supports can be rigid!?
4. How to make an area support
5. What can and cannot be simplified
6. Boundary conditions and Hooke’s law
7. Linear contact – the basics
8. How to define linear contact
9. When it is possible to ignore contact?
10. Typical solutions for contact and BC
11. Example 1: Cantilever
12. Example 2: Bolted connection
13. Example 3: Beam on area support
14. Example 4: Different rigidity supports
15. Conclusion -
Course 5 - FEA Loads
1. Realistic load values and codes
2. Characteristic and design loads
3. Point loads and reality
4. Force vs Moment
5. Gravity vs Pressure
6. Enforced deformations as load
7. Realistic load distribution
8. Load distribution: Part 1
9. Load distribution: Part 2
10. Load distribution: Part 3
11. Module 5: Conclusion -
Course 6 - FEA Meshing
1. Basic elements types
2. Beam Elements
3. Plate Elements
4. Solid Elements
5. Choosing element type
6. Higher-order elements
7. TRI vs QUAD
8. TET vs HEX
9. Model Simplifications
10. RBE – Rigid Body Elements
11. Plane Strain Elements
12. Mesh Refinement
13. Mesh Refinement: Case Study
14. Mesh Refinement: Challenge 1
15. Mesh Refinement: Challenge 2
16. Mesh and Mathematics (M&M!)
17. Mesh Quality Measures
18. Module 6: Conclusion -
Course 7 - FEA Analysis
1. Linear Analysis Setup
2. Solver vs Pre/Postprocessor
3. Linear Static Limitations
4. What does nonlinear material do?
5. What does nonlinear geometry do?
6. Contact
7. Beyond Linear Static
8. When it is safe to use linear static
9. Model Checking
10. Troubleshooting
11. Module 7: Conclusion -
Course 8 - FEA Post Processing
1. Business advice first!
2. Stress/Strain/Displacement
3. The Stress Map!
4. Stress averaging
5. Issues with stability
6. Dealing with stresses higher than yield
7. Strain as a measure of capacity
8. Deformations
9. Beams in FEA
10. Result verification
11. Verification with hand calculations!
12. Business side of the report
13. Technical side of the report
14. Module 8: Conclusion -
Course 9 - FEA Steel Plate Under Tension
1. Steel plate under tension
2. Geometry
3. Material properties
4. Boundary conditions
5. Loads
6. Meshing
7. Analysis
8. Post processing
9. Conclusion -
Course 10 - FEA Bolted Cantilever
1. Bolted Cantilever
2. Geometry
3. Material properties
4. Boundary conditions
5. Loads
6. Meshing
7. Analysis
8. Post-processing
9. Conclusion -
Course 11 - FEA Solid Bracket
1. Solid Bracket
2. Geometry
3. Material properties
4. Meshing
5. BC and contact
6. Loads
7. Analysis
8. Post-processing
9. Conclusion -
Course 12 - FEA Roof Rafter Stability
1. Roof rafter stability
2. Introduction: Stability design
3. Introduction: LBA
4. Introduction: LBA settings
5. Geometry
6. Supports / Loads / Mesh
7. Initial stability conclusions
8. Critical bending moment calculation
9. Critical bending moment in design
10. Bracing influence on stability
11. Developing model further: Part 1
12. Developing model further: Part 2
13. Verifying assumptions about bracings -
Course 13 - FEA Street Lamp
1. Street Lamp
2. Geometry
3. Geometry: Base: Part 1
4. Geometry: Base: Part 2
5. Geometry: Post: Part 1
6. Geometry: Post: Part 2
7. Geometry: The top part
8. Materials + Properties
9. Meshing
10. Meshing: Base plate
11. Meshing: Base plate: Bonus video
12. Meshing: Lamp post
13. Meshing: Top piece
14. Loads: Wind load according to EN 1991-1-4
15. Loads: Loading the model
16. Boundary conditions
17. BC: Avoid contact with line supports
18. BC: Dealing with stress concentrations
19. BC: Defining contact
20. Analysis
21. Post processing: Deformations
22. Post processing: Stress
23. Post processing: Stability
24. Post processing: Summary -
Final Notes & Certificate
1. Congratulations
2. Course evaluation survey
3. Your Personal Certificate
4. Rate this course
5. Related courses
Certification
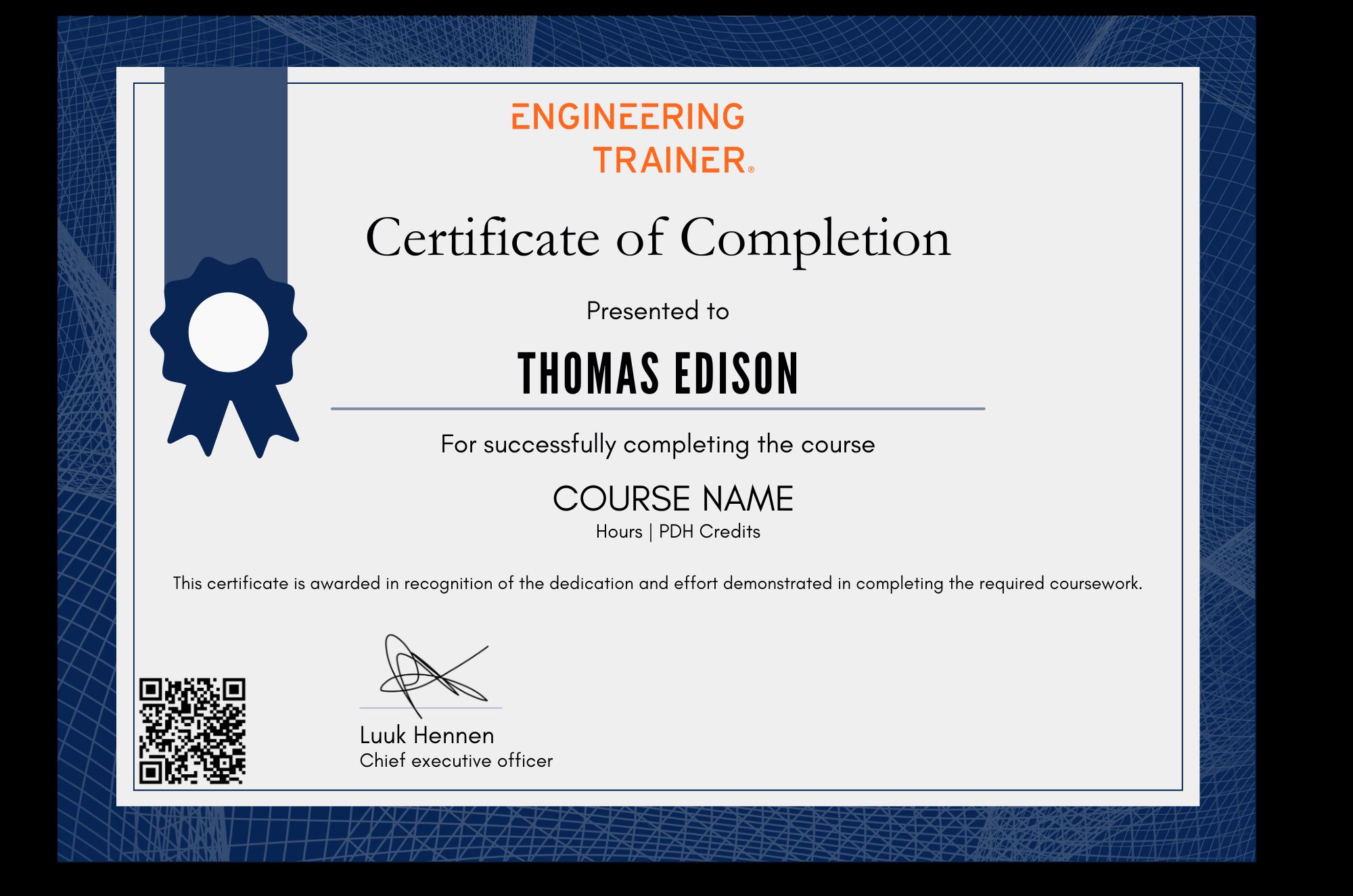
Contact us to Learn More
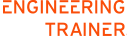
Why choose EngineeringTrainer
-
Unlimited Team-wide Access
-
Advance Technical Competences
-
Courses by Industry Authorities
Since using EngineeringTrainer our internal mentorship has a much more matured character.
Logan Chapman - COO at Chapman Consulting Inc.