Designing according to the EN13445 code
Why take this course?
This self-paced course covers the EN13445 design code for unfired pressure vessels, explaining key principles and equations behind the rules. Participants explore topics like area replacement, the Taylor and Forge method, stress evaluations, and vacuum collapse prevention. The course includes video lectures, quizzes, and offers a certificate with PDH credits to support your engineering proficiency.
What you'll learn
After these courses, you...
• understand the structure & scope of the code,
• understand the failure mechanisms considered in the code,
• are able to use the design rules for many components, amongst others cylindrical shells under internal & external pressure, openings and nozzles, flat ends and flange connections, heat exchanger tube sheets, rectangular shells and saddles and skirts,
• understand the role of Design by analysis (Finite Element Analysis) for EN13445 design,
• can identify the limitations of the design rules,
• know the important differences with the ASME BPVC VIII-1.
About the course
The EN13445 design code is the harmonized design code for unfired pressure vessel design under the Pressure Equipment Directive (2014/68/EU). Often the rules are applied using automated software packages and the engineer can lose the overview of the calculation being performed.
This course explains the fundamental equations and principles in these design rules. For example: What is the area replacement rule? How is the Taylor and Forge method applied? What inner-stiffener distance is required to prevent collapse under vacuum, and why? What is the difference between primary and secondary stresses, and how is this evaluated in the code?
Next to explaining the rules and how to apply them, participants are challenged on why a rule is formulated in a particular way and show important differences with ASME BPVC Section VIII Division 1 code.
Meet your instructor
Who should attend this course
• Those required to design pressure vessels as per the EN13445 and that want a solid overview and understanding of the design methods used in the code.• Engineers that already have experience with the EN13445 and that want to improve their understanding of the backgrounds for the different rules and methods applied in the code.
• Technicians involved in the production of EN13445 unfired pressure vessels that want a solid understanding of the design basis of their vessels.
Prerequisites
Technical background.Program & Details
-
Welcome
1. Welcome to the course
2. Your instructors
3. How to use this course
4. Personal Certificate requirements -
Course 1 - Introduction to EN 13445
1. Introduction
2. Scope
3. Materials
4. Brittle failure & creep
5. Module 1, Exercise 1
6. Welds and discontinuities
7. Fatigue analysis
8. Wall thickness & corrosion
9. Hydrostatic test pressure -
Course 2 - Stress Definition and Allowable Values
1. Intro: Stress definitions
2. Stress/Strain relationships
3. Stress/Strain relationships
4. Load cases
5. Maximum design stress
6. Module 2, Exercise 1 -
Course 3 - Shell under Internal Pressure
1. Intro: Shell design
2. Cylindrical shells
3. Spherical shells
4. Formed ends
5. Cones and conical sections
6. Cone to cylinder transition
7. Module 3, Exercise 1 -
Course 4 - Shells under External Pressure
1. Intro: Shell design
2. Cylindrical shells
3. Cylinder with Stiffeners
4. Module 4, Exercise 1
5. Cones
6. Shell ends -
Course 5 - Vessel Openings & Nozzles
1. Intro: Vessel openings
2. Pressure area method
3. Analysis of a set-on nozzle
4. Adjacent openings
5. Special cases
6. Module 5, Exercise 1 -
Course 6 - Designing Flat Ends and Flanges
1. Intro: Flat ends & flanges
2. Clause 10: Flat Ends
3. Flange types
4. Taylor-Forge flange check
5. Pressure rating method
6. Flange analysis
7. Module 6, Exercise 1 -
Course 7 - Design by Analysis
1. Intro design by analysis
2. What is design by analysis?
3. The equivalent stress
4. Module 7, Exercise 1
5. Stress Decomposition
6. Stress assessment
7. Stress decomposition
8. Instability & Buckling
9. Module 7, Exercise 2 -
Course 8 - Fatigue Assessment Methods
1. Intro: Fatigue assessment
2. Simplified fatigue check
3. Detailed fatigue assessment
4. Fatigue safety factor
5. Comparing fatigue checks
6. Module 8, Exercise 1 -
Course 9 - Heat Exchangers & Miscellaneous
1. Intro: Heat exchangers
2. Types of heat exchangers
3. Tubesheet thickness
4. Module 9, Exercise 1
5. Alternative methods
6. Bellows & expansion joints
7. Rectangular vessels
8. Applied forces & moments
9. Lifting lugs
10. Saddle supports
11. Supports -
Final Notes & Certificate
1. Congratulations
2. Course evaluation survey
3. Your Personal Certificate
Certification
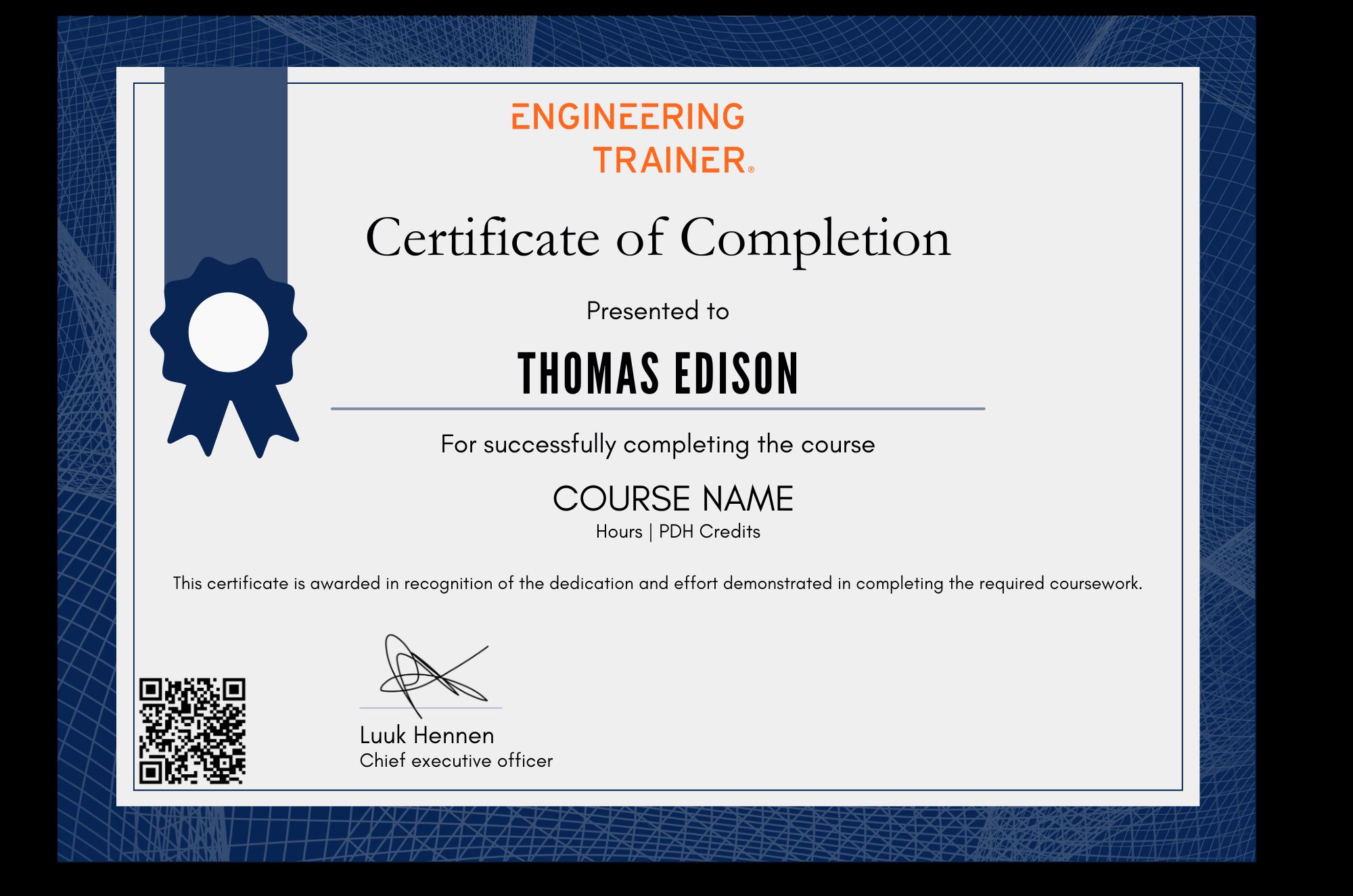
Designing according to the EN13445 code
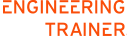
Why choose EngineeringTrainer
-
Unlimited Team-wide Access
-
Advance Technical Competences
-
Courses by Industry Authorities
Since using EngineeringTrainer our internal mentorship has a much more matured character.
Logan Chapman - COO at Chapman Consulting Inc.