Designing according to the ASME BPVC VIII-1 code
Why take this course?
This self-paced course offers an in-depth understanding of the ASME VIII-1 design code for pressure vessels. Explore fundamental equations, key principles, and design rules for shells, heads, nozzles, flanges, and more. The course includes video lectures, quizzes, and a certificate with PDH credits, providing a comprehensive learning path across 8 online modules for practical application and engineering insight.
What you'll learn
After these courses, you...
• Have a good overview of the structure and applicability of the ASME VIII-1 code,
• Understand the design rules conform ASME VIII-1 for standard pressure vessel components
(new bullet) Know the basis for the design rules in the ASME VIII-1
• Have performed multiple tutorials and quizzes to reinforce how to apply the ASME VIII-1 design rules,
• Are able to understand and recognise the ASME VIII-1 design rules in the output reports of pressure vessel design software.
About the course
The ASME VIII-1 design code is the most widely used design code for pressure vessel design. Often the rules are applied using automated software packages such as Compress or PVElite and the engineer can lose the overview of the calculation being performed.
This training course aims to explain the fundamental equations and principles in the design by rules approach in the ASME VIII-1 design code. For example: What is the area replacement rule for a nozzle sizing? How is the Taylor and Forge method applied for flange design? What is the minimum ligament length between nozzles and why? What inter-stiffener distance is required to prevent collapse under vacuum?
Topics in this training course on the ASME VIII-1 design code include many design features such as design of shells and heads under internal and external pressure, nozzles & openings, flange connections, heat exchanger, tubesheets, saddles and skirts.
As well as explaining the rules and how to apply them, you will be challenged on why a rule in the ASME VIII-1 is formulated in a particular way by referring back to the underlying engineering relationships.
This training course is a learning path which consists of 8 online courses each of which cover a different part of the ASME VIII-1 design code for pressure vessels.
Meet your instructor
Who should attend this course
• Those designing pressure vessels with ASME BPVC VIII Div. 1.• Engineers which need to have a solid understanding of the approaches used in the code.
• Those that wish to understand the backgrounds and design basis for the code rules.
Prerequisites
Technical background.Program & Details
-
Welcome
1. Welcome & Your instructor
2. Content overview
3. How to use this course -
Course 1 - Introduction to ASME BPVC VIII-1 and Related Physical Concepts
1. Introduction and Agenda
2. ASME VIII-1 Code Coverage: Outline and Build-up
3. Materials Aspects and Codes
4. ASME Section 2 part D: Material Tables
5. Weld Joint Efficiency in ASME Section 8, division 1
6. Non Destructive Testing related to Joint Efficiency Factor
7. Design Loads - Part 1, 2 & 3
8. U-stamping for Pressure Vessels
9. Code Design Stresses and Allowables
10. Fatigue Design in ASME VIII-1
11. Brittle Fracture: Physical Concepts
12. Analyzing Brittle Fracture as per the ASME BPVC VIII-1
13. Module 1, Exercises 1: Weld Joint Efficiencies
14. Module 1, Exercise 2: Determining the MDMT -
Course 2 - Stress Concepts and Allowables
1. Stress-Strain Relationships and Concepts
2. Material Stresses for Cylindrical Shells
3. Load Cases and Failure Modes
4. Maximum Allowable Values for the Design Stress -
Course 3 - Component Subject to Internal Pressure
1. Introduction and Agenda
2. Cylindrical Shells under Internal Pressure
3. Spherical Shells and Formed Ends
4. Cones and Conical Sections under Internal Pressure -
Course 4 - Component Subject to External Pressure
1. Introduction and Agenda
2. Introduction to Buckling for Pressure Vessels
3. Buckling Examples and Illustrations
4. Axial Compression Loads as per ASME VIII-1
5. Compressive Stress: Allowable Value
6. Cylindrical Shells under External Pressure
7. Thin Walled Shells: Buckling Evaluation
8. Buckling Critical Length as per ASME VIII-1
9. Thick walled Shells: Buckling Evaluation
10. What are Stiffener Rings?
11. Using Stiffener Rings as per ASME VIII-1
12. Vessel Heads under External Pressure - Part 1 & 2 -
Course 5 - Openings in Shells
1. Introduction and Agenda
2. Shell Openings: An Introduction
3. Area Replacement Rule as per ASME VIII-1
4. Area Replacement Rule: Step 1, 2, 3 & 4
5. Ligament Efficiency Rules as per ASME VIII-1
6. Ligament Efficiency Rules: Diagonal Lines -
Course 6 - Flat Heads and Flanges
1. Introduction and Agenda
2. Flat Plates, Covers, Flanges and Design Rules in ASME VIII-1
3. Bolted Connections as per ASME VIII-1
4. Gasket Selection for Flanges
5. Bolt Evaluations for Flanges
6. Design of Bolted Flanges and Associated Calculations
7. Calculation Steps for Bolted Connections - Part 1 & 2
8. Equivalent Pressure Rule for Flange Evaluation -
Course 7 - Heat Exchangers
1. Introduction and Agenda
2. Types of Heat Exchangers and Analysis Methods
3. Tubesheet Properties: Calculating Effective Values
4. Tubesheet Thickness and Related Calculations
5. Alternative Methods for Tubesheet Design -
Course 8 - Vessels of Non-Circular Cross Section and Half Pipe Jackets
1. Rectangular Vessels as per ASME VIII-1
2. Openings in Non-Circular Vessels
3. Half-Pipe Jackets as per ASME VIII-1 -
Final Notes & Certificate
1. Congratulations
2. Course evaluation survey
3. Your Personal Certificate
4. Rate this course
5. Related courses
Certification
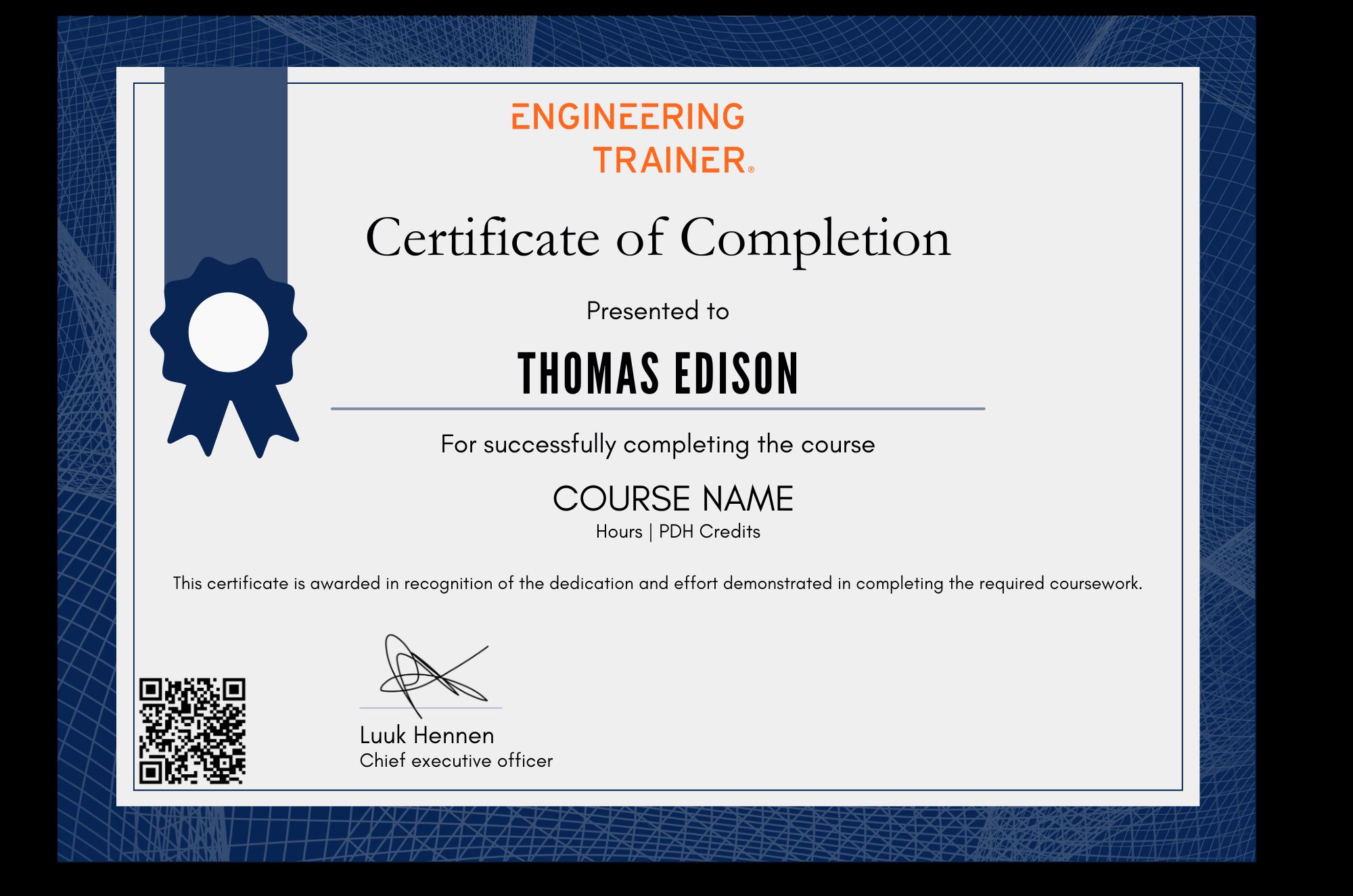
Designing according to the ASME BPVC VIII-1 code
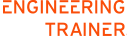
Why choose EngineeringTrainer
-
Unlimited Team-wide Access
-
Advance Technical Competences
-
Courses by Industry Authorities
Since using EngineeringTrainer our internal mentorship has a much more matured character.
Logan Chapman - COO at Chapman Consulting Inc.