Pipework Vibration
Why take this course?
Understand causes and mitigation of pipework vibration-induced fatigue. Covers screening, assessment, and corrective techniques. Emphasis on LOF calculations. This course includes live sessions and provides a certificate with PDH credits.
What you'll learn
After this course, you...
• have a good understanding of key vibration fundamentals, including the damaging effect of resonance,
• understand the main causes and consequences of pipework vibration,
• know about Qualitative and Quantitative Assessment methods for calculating ‘Likelihood of Failure’ (LOF) for Main Lines, Small Bore Connections and Thermowells – supported by worked examples,
• understand how to perform a visual assessment of pipework to be able to identify and prioritise potential areas of concern,
• know about portable vibration measurement instrumentation and how to perform basic vibration measurements and assessments against Energy Institute limits.
• understand the value of strain measurements and how to perform basic fatigue life estimates based on BS 7608.
• understand what constitutes ‘good practice’ for avoidance of vibration induced fatigue.
• have seen common pipework vibration solutions, including the selection and implementation of remedial pipe supports, including braces, visco• dampers and dynamic absorbers.
About the course
Many normal process operations can cause vibrations in pipework, due to a variety of excitation mechanisms, which over time can lead to fatigue fractures resulting in leaks. Vibration Induced Fatigue failures occur due to the progressive growth of fatigue cracks in welded connections due to fatigue mechanism.
Failure occurs weeks, months or often years after the first sign of the crack. At this point the crack has grown fully through-wall, resulting in a leak, often during an extreme event such as a pipe surge or pressure spike. Such fractures could lead to serious incidents involving major injury, fire, explosion or pollution. Many serious pipe vibration issues can be easily detected using simple vibration screening techniques and can be avoided by adopting industry best practice.
This course will provide a detailed introduction into pipework vibration to raise the knowledge, skills and confidence of engineers to be able to perform their own visual, basic vibration and strain surveys and assessments. It will also provide a good overview of common remedial solutions and other specialist techniques, and provide additional information on the selection and implementation of Braces, Visco-dampers and Dynamic Vibration Absorbers for corrective actions.
Emphasis is placed on both practical and theoretical aspects of the subject and covers in detail Quantitative Assessment Methods for the calculation of Likelihood of Failure (LOF) for main lines, small bore connections and Thermowells.
Who should attend this course
Operators, Technicians, Engineers, Supervisors and Managers involved in any of the following areas:• Asset Integrity, Mechanical Inspection and Risk Based Inspection (RBI)
• COMAH Compliance and Reliability
• Pipe Stress and Piping Design
• Plant Integrity, Plant Maintenance, Plant Safety and NDT
• Process Engineering
Prerequisites
Attendees do not require any prior knowledge of pipework vibration.Ideally the attendees will have a good understanding of the use of pipework within process plants and have a technical aspect to their roles.
Good proficiency in basic mathematics.
Good understanding of the English language.
Program & Details
-
Course Introduction
1. Trainer Intro
2. VibTech Intro
3. Tips with using MS Teams
4. Course Format and Timescales
5. Multiple Choice Tests -
Introduction to Pipework Vibration
1. Overview of Pipework Vibration
2. Introduction to Energy Institute publication ''Guidelines for the avoidance of vibration induced fatigue failure in process pipework'', 2nd edition, 2008 (current) -
Vibration Basics
1. Definitions
2. Units of measurement
3. Introduction to Spectra
4. Natural Frequency
5. Forced Vibration
6. Resonant Vibration -
Main Causes & Consequences of Pipework Vibration
1. Identifying the main excitation mechanisms causing pipework vibration:
- Flow Induced Turbulence
- Mechanical Excitation
- Pulsation
- Acoustic Induced Vibration
- Surge & Momentum Change
- Cavitation & Flashing
- Small Bore Connections
- Thermowells
2. Understanding the consequences which could lead to failures:
- Fatigue
- Fretting -
Fatigue Analysis
1. Explanation of the key factors affecting fatigue life
2. Effects of Stress
3. Fatigue Endurance curves
4. Fatigue of Welds
5. Effects of Corrosion
6. Intro to BS 7608 -
Basic Assessment Methodology
1. Introduction to the various tools and techniques
2. Suggested sequence of events for investigation and assessment of risk of Pipework Vibration Fatigue -
Introduction to Quantitative and Qualitative Assessment
1. Intro to Qualitative and Quantitative Assessment
2. Method for assessment of potential excitation mechanisms. -
Main line Quantitative LOF Assessment - Flow Induced Vibration (FIV)
1. Quantitative Assessment method for assessing the risk of Failure due to Flow Induced Turbulence
2. Primarily to understand key factors and their significance -
Main line Quantitative LOF Assessment - Mechanical Excitation
1. Quantitative Assessment method for assessing the risk of Failure due to Mechanical Excitation
(e. g. Direct excitation from Machines or indirectly from other pipework)
2. Primarily to understand key factors and their significance -
Main line Quantitative LOF Assessment - Pulsation
1. Quantitative Assessment method for assessing the risk of Failure due to 3 types of tonal pulsations due to acoustic resonance
(reciprocating machines, rotating machines and dead-leg branches).
2. Primarily to understand key factors and their significance -
Main line Quantitative LOF Assessment - High Frequency Acoustic Excitation
1. Quantitative Assessment method for assessing the risk of Failure due to high frequency Acoustic Induced Vibration (AIV)
2. Primarily to understand key factors and their significance -
Main line Quantitative LOF Assessment - Valves
1. Quantitative Assessment method for assessing the risk of Failure due to Surge and Momentum change associated with fast acting valves
2. Primarily to understand key factors and their significance -
Main line Quantitative LOF Assessment - Cavitation and Flashing
1. Quantitative Assessment method for assessing the risk of Failure due to Cavitation & Flashing in liquid systems
2. Primarily to understand key factors and their significance -
Quantitative Assessment of LoF
Review including Multiple Choice Questions
-
SBC Quantitative Assessments
1. Quantitative Assessment method for assessing the risk of Failure of Small Bore Connections (SBC), considering Geometric Factors and Location Factors for 4 generic configurations
2. Primarily to understand key factors and their significance -
Thermowell Quantitative LOF Assessment
1. Quantitative Assessment method for assessing the risk of Failure of Thermowells due to flow induced vortices caused by flow of fluid past thermowell
2. Primarily to understand key factors and their significance
3. Introduction to alternative standard ASME PTC B19. 3TW-2010 -
Visual Inspection
1. Learning Visual Survey techniques to identify pipework with increased risk of failure
2. Learning what to look for to identify good and bad practice Supported by library photo
3. Opportunity to try to identify some common examples of Bad Practice from Photo Library -
Basic Vibration Survey
1. Learning Vibration Survey techniques to identify pipework with increased risk of failure
2. How to setup a vibration meter and where to take measurements
3. How to process results and how to interpret results -
Small Bore Tubing - Latest Recommendations
Latest Energy Institute recommendations for instrument tubing covering protection against vibration for pipework and structure mounted instrumentation and allowance for large scale deformations (thermal expansion)
-
Definition of the "Concern Factor"
Introduction to a new 'Concern factor' for assessing and ranking Pipework Vibration results.
-
Visual and Vibration Assessment
Review including Multiple Choice Questions
-
Specialist Techniques
Introduction to other pipework vibration assessment techniques, including:
- Strain Gauges
- FEA
- Motion Amplification
- Operating Deflection Shape Analysis
- Modal Analysis -
Strain Measurement and Fatigue Assessment
1. Introduction to Strain Gauges, including where to measure strains
2. Fatigue Assessment methods -
Main line Corrective Actions
1. Review of corrective actions for solving vibration problems on Main Lines, including:
2. Flow Induced Turbulence
3. Mechanical Excitation
4. Pulsation
5. Acoustic Induced Vibration
6. Surge & Momentum Change
7. Cavitation & Flashing -
Visco-Elastic Dampener Selection
Considerations for the use of Visco-Elastic Dampers to solve Main Line vibration issues.
-
Small Bore Connection Corrective Actions
1. Review of Corrective actions for solving vibration problems on Small Bore Connections (SBCs)
2. Introduction to Easy-Brace® universal SBC solution
3. Design considerations, relating to brace stiffness, the use of I-beams and the problems with thin-walled pipes -
Quantitative Assessment Tool
Introduction to VibTech Quantitative Assessment Tool (QAT) - performs all EI LOF calculations in Sections T2, T3 & T4 of EI Guidelines
-
Review Corrective Actions
Review including Multiple Choice Questions
-
Worked Examples of LOF calculation
1. Worked Example - Main Line LOF - Gas Compression System
2. Worked Example - SBC LOF calculation Type 1
3. Worked Example - SBC LOF calculation Type 2
4. Worked Example - SBC LOF calculation Type 3 -
Corrective Action Case Studies
1. Corrective Actions Case Studies (AVT) - Easy Brace
2. Corrective Actions Case Studies (AVT) - Visco-Damper
3. Corrective Actions Case Studies (AVT) - Dynamic Vibration Absorber -
Good Design Practice Summary
1. Summary of Good Practice features for Main Lines, SBCs and Tubing
2. Most common mistakes -
Conclusions
Summary of key learnings during the course
Certification
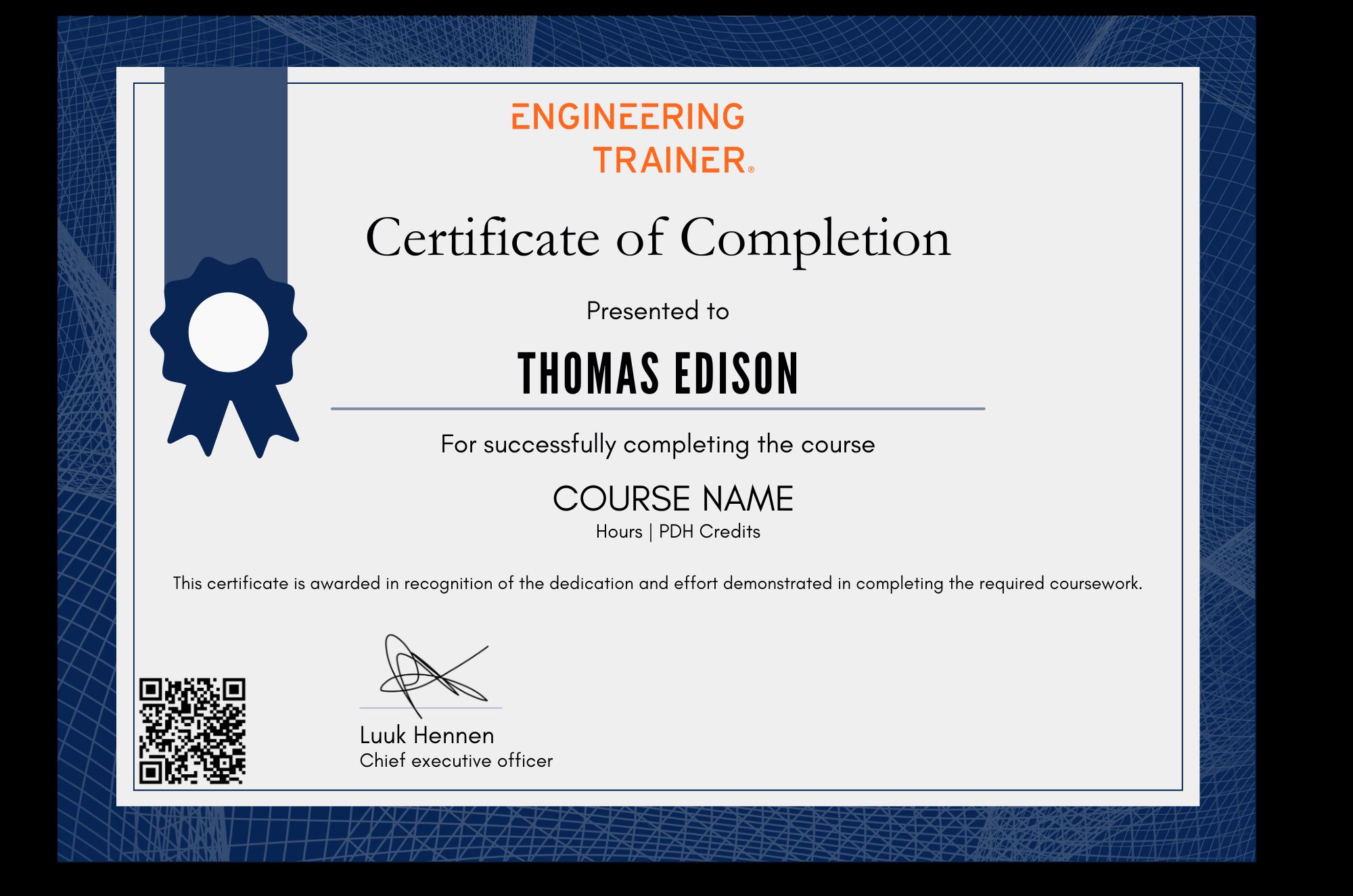
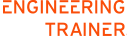
Why choose EngineeringTrainer
-
Unlimited Team-wide Access
-
Advance Technical Competences
-
Courses by Industry Authorities
Since using EngineeringTrainer our internal mentorship has a much more matured character.
Logan Chapman - COO at Chapman Consulting Inc.