Fitness for Service Assessment According to API 579-1/ ASME FFS-1
Why take this course?
This course offers an in-depth exploration of Fitness for Service (FFS) assessment based on API 579-1/ASME FFS-1 standards. Participants learn to evaluate aging or damaged equipment through stress analysis, damage identification, and flaw assessment. The course includes video lectures, quizzes, and awards a certificate with PDH credits upon completion.
What you'll learn
After this course, you...
• can recognise and categorise various degradation mechanisms impacting equipment integrity,
• understand the methodologies and guidelines outlined by API 579-1/ASME FFS-1 for assessing equipment fitness for service,
• have mastered techniques for flaw assessment, including crack evaluation, corrosion and pitting assessment, and flaw characterisation,
• understand the fundamentals of failure including plastic collapse, fracture failure, fatigue damage and high-temperature component life assessment,
• know how to perform a Brittle Fracture Analysis: can analyse the susceptibility to brittle fracture and implement mitigation strategies,
• be able to use the industry standard techniques for estimating remaining life and predicting equipment reliability,
• know how to navigate through the intricacies of Level 1 and 2 assessments as per API 579-1/ ASME FFS-1 guidelines,
• be able to develop effective mitigation plans and decision-making based on FFS evaluations and their outcomes,
• have engaged with practical case studies and scenarios for hands-on application of API 579-1/ ASME FFS-1 principles.
About the course
Fitness for Service (FFS) assessment, particularly guided by API 579-1/ASME FFS-1, has emerged as a crucial framework in the realm of structural integrity management. In today's industrial landscape, where aging equipment and infrastructure pose significant challenges, mastering API 579-1/ASME FFS-1 becomes imperative.
This course delves into the core principles and methodologies of API 579-1/ASME FFS-1, empowering engineers, inspectors, and asset integrity professionals to evaluate, analyse, and make informed decisions regarding the fitness of aging or damaged equipment. As equipment reaches different stages of its service life, understanding how to effectively assess and address flaws or damages becomes pivotal. This course equips participants with the knowledge and tools needed to safeguard equipment reliability, minimize downtime, optimize maintenance strategies, and ensure operational safety. By navigating through practical case studies and real-world scenarios, attendees gain actionable insights to address critical challenges and enhance the lifespan and performance of industrial assets.
This comprehensive course offers a deep dive into the essential facets of Fitness for Service (FFS) assessment aligned with the API 579-1/ASME FFS-1 standards. Beginning with an exploration of FFS fundamentals, participants embark on a journey through crucial topics such as stress analysis, damage mechanisms identification, assessment techniques, and structural integrity evaluation methodologies prescribed by API 579-1/ASME FFS-1. Delving into practical case studies and hands-on exercises, attendees gain proficiency in flaw assessment, corrosion evaluation, fracture assessment, and the intricacies of remaining life estimation.
The course consists of 26 hours of live sessions with the instructor. All training content is provided through your EngineeringTrainer account.
Who should attend this course
• Engineers (Mechanical, Structural, or Materials): Seeking expertise in assessing equipment integrity and evaluating fitness for continued service.• Inspection and Integrity Professionals: Involved in asset integrity management, inspection planning, and structural assessment.
• Maintenance and Reliability Engineers: Focused on optimizing maintenance strategies and ensuring equipment reliability.
• Asset Managers and Operations Personnel: Responsible for ensuring operational safety and efficiency of industrial equipment.
• Quality Assurance/Quality Control (QA/QC) Professionals: Interested in enhancing quality assessment methods and reliability evaluations.
Prerequisites
There are no specific prerequisites for this course. Having a foundational understanding or appreciation of pressure equipment could aid participants in grasping concepts more effectively during the course.Program & Details
-
Fitness for service overview
Live
1. An introduction to FFS
2. Real case scenarios
3. FFS common codes and standards
4. Scope and structure of API 579-1/ASME FFS-1
5. Three levels of assessment
6. Data and information required
7. Important concepts: RSF -
Stress Analysis in Pressure Equipment
Live
1. Basic Concepts
2. Stress in Pressure Equipment
3. ASME B&PV design concept
4. Allowable Stress
5. Primary and Secondary Stresses
6. Residual Stress
7. Finite Element Analysis
8. Strain Measurement
9. Work Examples -
Failure Modes and Damage Mechanisms
Live
1. Failure modes
2. Flaw characterisation
3. Weld morphology
4. Pre-service flaws
5. In-service damage mechanisms
6. Work Example -
Inspection and Non-Destructive Examination (NDE)
Live
1. Introduction to inspection techniques
2. Inspection effectiveness
3. Conditional probability
4. Work Examples -
Assessment of Existing Equipment for Brittle Fracture (Part 3)
Live
1. Damage Identification
2. Real-life case study
3. Charpy Ductile to Brittle Transition Curves
4. Minimum Allowable Temperature (MAT) and Critical Exposure Temperature (CET)
5. Part 3 Assessment Techniques and Acceptance Criteria
6. Work Example -
Assessment of General Metal Loss (Part 4)
Live
1. Damage Identification
2. Types of pressure equipment based on ASME B&PV codes
3. Part 4 Assessment Techniques and Acceptance Criteria
4. Work Example -
Assessment of Local Metal Loss (Parts 4 and 5)
Live
1. Damage Identification
2. Critical thickness Profile (CTP)
3. Part 4 Assessment Techniques and Acceptance Criteria for Local Metal Loss
4. Part 5 Assessment Techniques and Acceptance Criteria for Local Metal Loss
5. Work Examples -
Assessment of Pitting Corrosion (Part 6)
Live
1. Damage Identification
2. Part 6 Assessment Techniques and Acceptance Criteria
3. Work Example -
Hydrogen Blisters and Hydrogen Damage Associated with HIC and SOHIC (Part 7)
Live
1. Damage Identification
2. Fundamentals of Hydrogen damage
3. Part 7 Assessment Techniques and Acceptance Criteria -
Assessment of Weld Misalignment and Shell Distortions (Part 8)
Live
1. Damage Identification
2. Part 8 Assessment Techniques and Acceptance Criteria -
Assessment of Crack-Like Flaws (Part 9)
Live
1. Damage Identification
2. Real life case study
3. Fundamentals of Fracture Mechanics
4. Fracture Toughness
5. Failure Assessment Diagram (FAD)
6. Part 9 Assessment Techniques and Acceptance Criteria
7. Work Examples -
Assessment of Components Operating in the Creep Range (Part 10)
Live
1. Damage Identification
2. Real-life case study
3. Fundamentals of high temperature material behaviour
4. Larson-Miller Parameter
5. Part 10 Assessment Techniques and Acceptance Criteria
6. Work Example -
Assessment of Fire Damage (Part 11)
Live
1. Damage Identification
2. Part 11 Assessment Techniques and Acceptance Criteria
3. Work Example -
Assessment of Dents, Gouges, and Dent-Gouge Combinations (Part 12)
Live
1. Damage Identification
2. Part 12 Assessment Techniques and Acceptance Criteria
3. Work Example -
Assessment of Laminations (Part 13)
Live
1. Damage Identification
2. Part 13 Assessment Techniques and Acceptance Criteria
3. Work Example -
Assessment of Fatigue Damage (Part 14)
Live
1. Damage Identification
2. Real-life case study
3. Fundamental of fatigue damage
4. Cycle counting
5. S-N curves
6. Fatigue Crack Growth and Paris Power Law
7. Part 14 Assessment Techniques and Acceptance Criteria
8. Work Examples
Certification
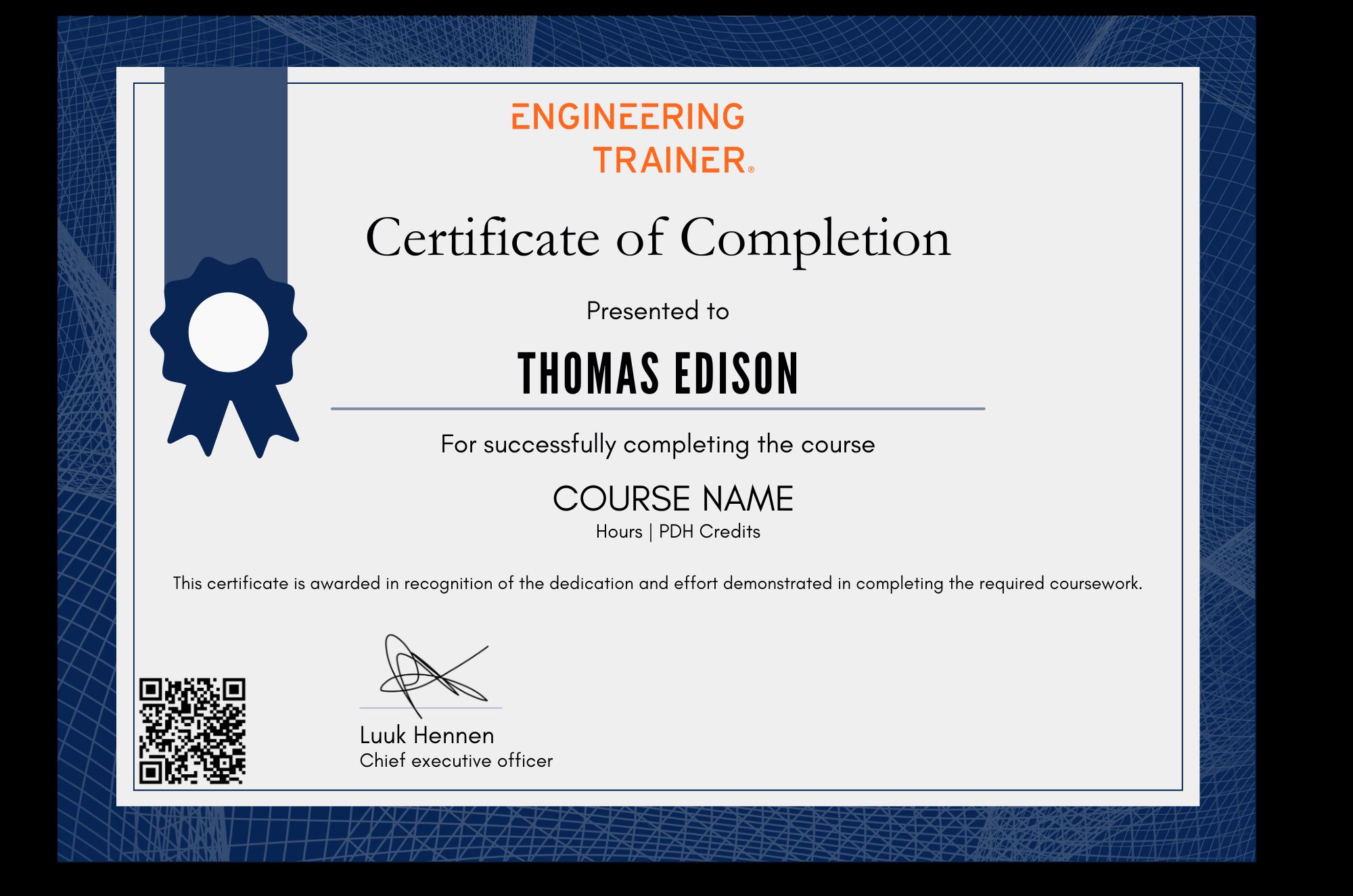
Fitness for Service Assessment According to API 579-1/ ASME FFS-1
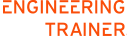
Why choose EngineeringTrainer
-
Unlimited Team-wide Access
-
Advance Technical Competences
-
Courses by Industry Authorities
Since using EngineeringTrainer our internal mentorship has a much more matured character.
Logan Chapman - COO at Chapman Consulting Inc.